安全・品質
品質管理の基本!物流現場におけるQC7つ道具の考え方
2020.12.09
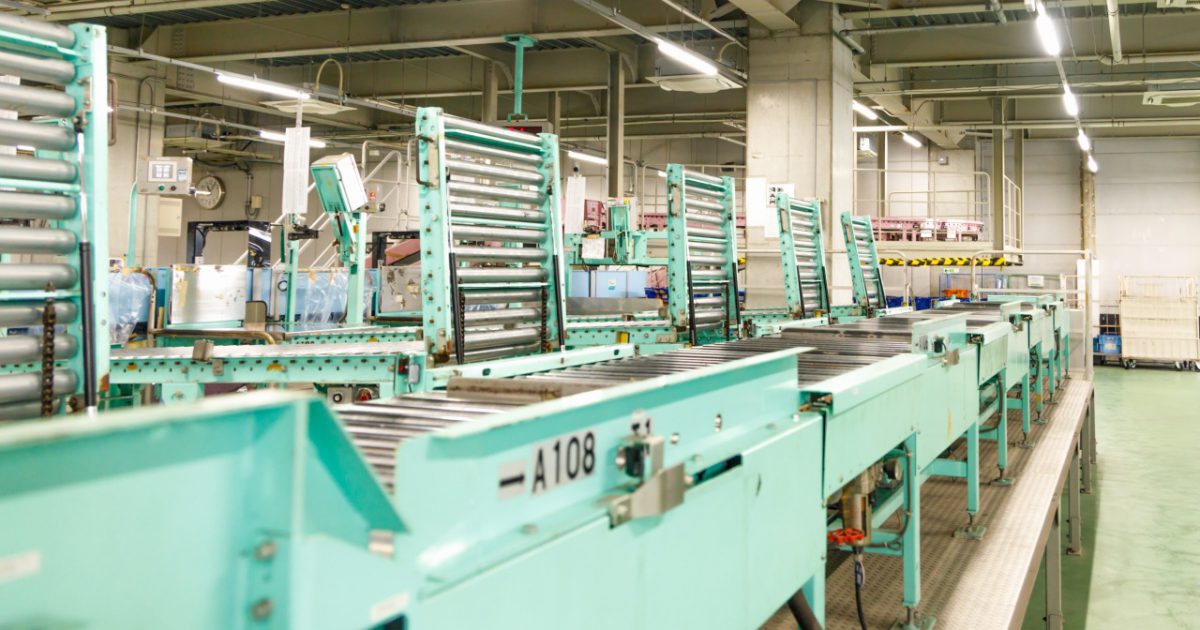
物流現場でお勤めの皆さん、「QC7つ道具」というものをご存知でしょうか。QC7つ道具とは、品質管理における7つの分析手法を指します。もともと製造現場における品質管理から出てきたもので、「QCサークル」という職場内の小集団で品質向上・改善に取り組む活動と連動して確立、発展してきました。
この記事では製造現場から出てきたQC7つ道具をどのように物流倉庫内で転用・応用して使っていくかという視点から解説していきます。
品質管理(QC)の基本的な考え方
品質管理の基本は数値の把握
品質管理(Quality Control)とは、製品やサービスを決められた基準に対して過不足なく製造・提供するように管理することを指します。物流においては、事前に顧客と取り決めたサービスレベルを満たすように物流業務を行うことを指します。
品質管理の基本は数値の把握です。数値化しないと基準を満たしているか満たしていないかを誰も判断することができませんし、何に取り組んで何を改善すればいいのか見当がつきません。
QC7つ道具は品質向上と維持のための手法
QC7つ道具は品質向上と維持のために考え出された道具です。数値をとったり、とった数値の情報を整理したりするための手法です。
問題発見と原因発見
問題の「見える化」
品質管理を行う上では非常に重要なことなのですが、発見していない問題は解決できません。今の状態は基準をクリアしているのか、していないのか。基準を大きく超える過剰なサービスにコストを使っているのではないか。そうしたことを正しく認識するためにはまず問題を「見える化」する必要があります。
課題は発見したら7割は解決しているという言葉もあります。課題を発見することが品質向上における最初の鍵となります。
原因の発見
先ほどは「発見していない問題は解決できない」と言いましたが問題を発見したとしても原因がわからなければやはり問題を解決することはできません。
問題が起きていることを把握したら、起こっていることを深堀りし、問題を起こしている原因を探る作業が必要です。
これらの問題発見と原因発見のためのツールが以下のQC7つ道具です。8つあります。
・チェックシート
・パレート図
・グラフ
・管理図
・ヒストグラム
・特性要因図
・散布図
・層別
ちなみにどうしてQC7つ道具が8つあるのかはわかりませんでした。文献によって「層別」を外していたり、「管理図」をグラフの中に入れていたりバリエーションはありましたがこの記事では8つ紹介します。
主に問題発見のための道具
チェックシート
チェックシートとは、調査を行うために現場の作業者に記入してもらうシートのことです。例えばエリアごとの破損発見数や破損の種類を発見ごとに都度記入するシートなどがそれです。
記入するのに作業者の時間と手間が取られるので調査の目的を明確にしてできるだけ手間を掛けずに記入できるように工夫する必要があります。物流現場であれば主に商品破損に関する調査で使うことが多いかもしれません。
パレート図
パレート図は様々な要素の中から何に優先的に着手すべきかを決めるために使うツールです。下の図はある倉庫における一日あたりの工数のパレート図です。
例えば生産性向上に取り組もうとしたときに、どの工程から着手すべきでしょうか。図を見ると、全体の工数のうちの70%近くは梱包と棚入れに使われています。一方棚整理は全体のうちわずか3%の5時間の工数でしかありません。仮に棚整理の工数を50%削減できたとしても2.5時間、全体のうちのおよそ1.5%の成果しかでませんが、もし梱包の工数を50%削減できれば30時間、全体の20%の工数を削減することができます。
このように、パレート図を用いることでどんなことに取り組めば大きな改善効果が見込めるのかを検討することができます。
グラフ
データは数値のままだと変化や異常を捉えることや比率を把握するのが難しいです。そうした場合、折れ線グラフを使うことで、時間的変化やなんらかの異常な状態を一目で察知することができます。また円グラフや帯グラフを用いることで比率、割合を直感的に把握することができます。
グラフには以下の種類があります。
・折れ線グラフ
・棒グラフ
・円グラフ
・帯グラフ
・レーダーチャート
管理図
管理図は、主に製造現場での不良品率の管理に使う手法です。あまり物流現場で使うことは想定されない手法ですが、QC7つ道具として紹介されることが多いので参考までに紹介します。
管理図は、ものづくりの現場で発生する「ばらつき」を管理する手法で、一定確率で発生する「偶然によるばらつき」と「異常原因によるばらつき」を区別するために用います。時系列の折れ線グラフを作成し、事前に算出した上下の管理限界線を超えていないか、規則性を持った動きをしていないかなどをチェックします。
管理限界線を超えていたり、規則性を持った動きをしたりしている場合、なんらかの異常があることを疑って工程を検査します。
この手法は一定の「あるべき不良品率」が安定した工程を想定したものであり、高い品質を崩さないために使われる手法と言えます。明らかな改善点がある場合、管理限界線、つまり管理上許容できるばらつきの度合いを適切に設定することができません。立ち上げ初期や明らかに改善点がある場合には、時系列の折れ線グラフを用いたほうが手間もかからずシンプルに可視化できます。
ヒストグラム
ヒストグラムとは、データの分布状況を把握するためのグラフの一種です。データを区間に区切り、その区間に出てくる数値の個数を棒グラフで表します。
製造現場においては製品の仕様に対しての「ばらつき」の性格を捉えるために使います。これも管理図同様に物流現場ではあまり使い所は少ないかもしれません。
どのように数値がばらついているかを把握することで異常がないか、想定していない要因によって分布がずれていないかなどを確認します。データの形を視覚的に捉える方法のひとつです。
主に原因発見のための道具
特性要因図
特性要因図は問題に対する要因を魚の骨のような図の形に整理した図のことです。別名フィッシュボーンチャートと呼ばれます。
要因を漏れなく抽出し、分解・整理を行うことができます。
特性要因図の例
特性要因図は特性に影響を及ぼす可能性のあるものを書き出し、可能性が高いと判断したものから順番に検証を行っていきます。表面的な対策を闇雲に実施することを避け、真の問題点の見落としを防ぐための手段です。そのため、同じ内容のものが2つ出てきたり、2つの分類にまたがった内容のものが出てきたりしても構いません。
散布図
散布図は2つのデータの間の関係を調べる手法の1つです。
架空の国語と算数のテストの結果の関係を散布図にしました。このようにデータのまとまりが右上がりになっていることを「正の相関がある」と言います。反対に右下がりになっていれば「負の相関がある」といいます。ばらつきが少なくデータのかたまりが直線に近いほど「相関が強い」「強い相関がある」と表現します。エクセルを使うとかんたんに近似直線や近似曲線を描画することができます。
物流現場においても様々な使い方が考えられます。ひとつには過去の傾向から未来の状況を予測するために使うこともできます。
極端な例ですが、例えばエアコンの出荷を行う物流現場であれば、過去の夏場の気温とエアコンの出庫数のデータから翌日の出庫数を大まかに予想して人員計画を組む、などが考えられます。
層別
層別はグラフなどの特定の分析手法ではなく、データを分析する際の考え方です。データを分析するときに、設備別、作業者別、商材のサイズ別といったようにデータを分けることを層別と言います。分けたデータを使ってこれまで見てきた折れ線グラフや散布図などを使って分析します。
3台の機械のうち1台に不具合があったとして、3台分がまとまっているデータでは何が原因かわかりません。それぞれを分離したデータを見ることによってはじめて3台のうちの1台に不具合があるということが見えてきます。
層別でデータを分けるためには調査の段階で分けられるようにデータを取得しておく必要性があります。
まとめ
QC7つ道具について物流現場の目線からかんたんに概要を解説しました。課題を発見し、原因を見つけるための手助けとなる道具ですので、これらを使いこなせるようになれば一段上の品質管理につながるかもしれません。
それぞれの手法についての詳しい使い方は今後解説を行っていく予定ですので、ぜひ物流現場通信をブックマークに追加していただければと思います。QC7つ道具以外にも生産性向上やコンプライアンスに関する知識なども発信しております。