生産性
現場のムダな滞留が見えてくる? 物流と「リトルの法則」
2025.02.21
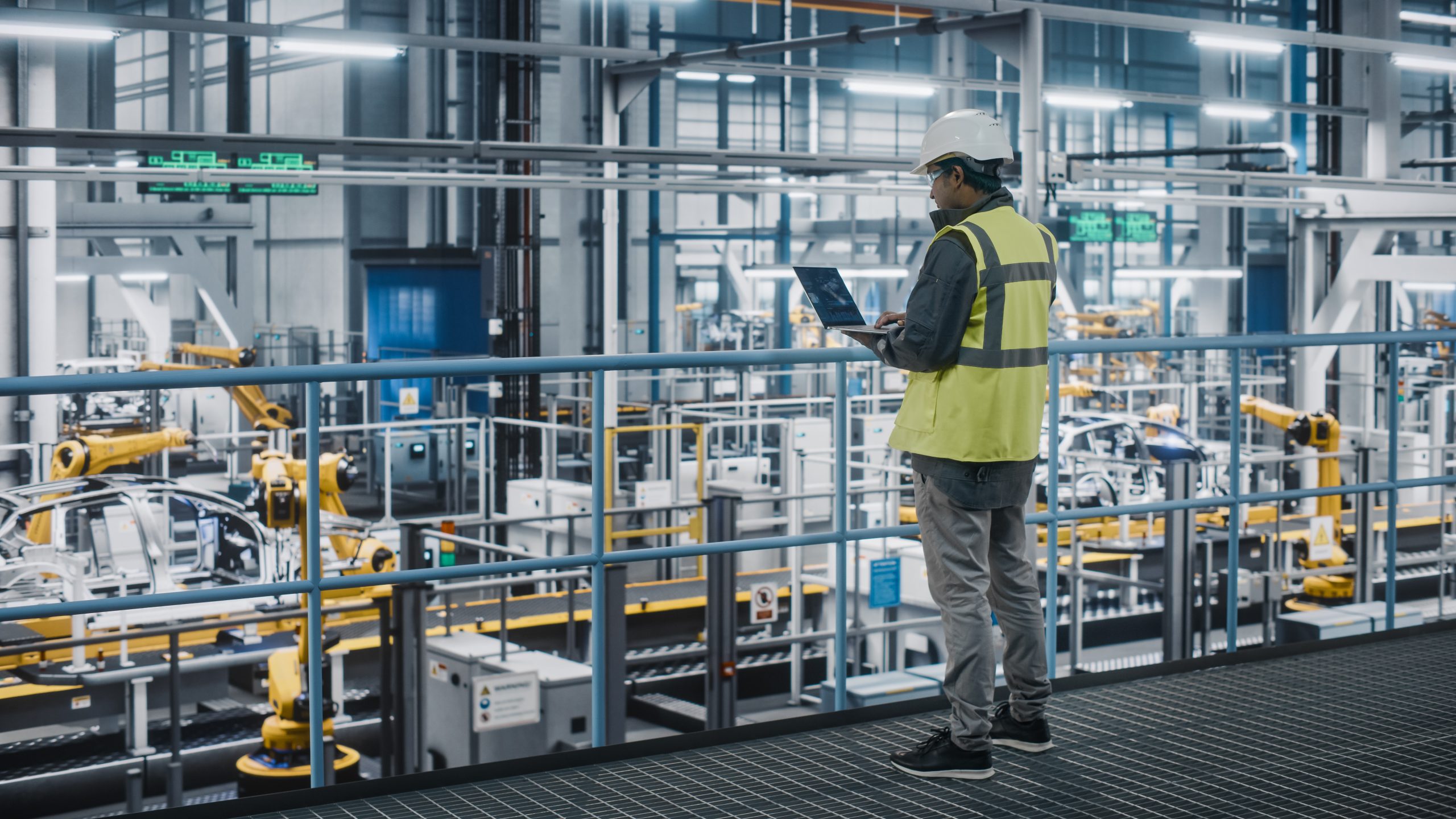
突然ですが、行列の待ち時間の推測に用いられる「リトルの法則」という数式をご存じでしょうか。
物流に何の関係が?と思われるかもしれません。
でも、この法則が倉庫内の作業効率改善への扉を開くとしたら…?
今回は、難しそうな印象の数学が物流業務にどう結びつくのか、なるべくわかりやすく説いていきます。
「リトルの法則」とは?
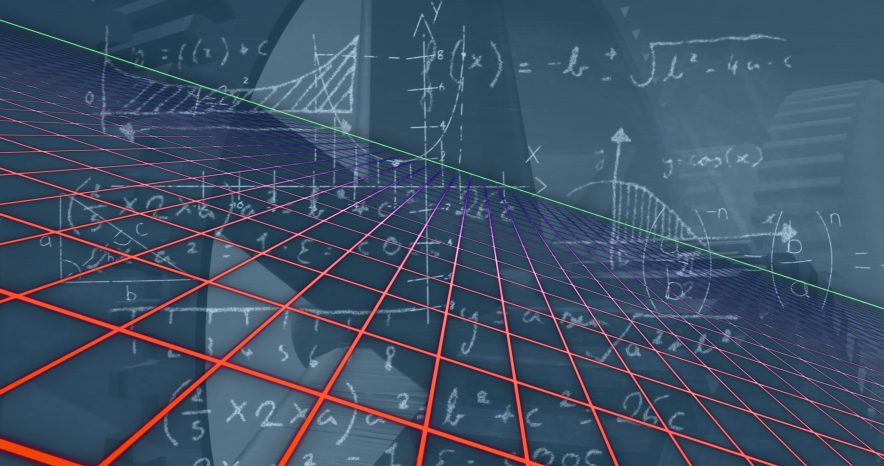
評判のグルメ・スポット、話題のアトラクション、スーパーやコンビニの会計待ちなど、普段の生活の中で行列に並んだ経験は誰にだってあるはず。
待つのが苦手な人だけでなく、待つのは苦にならないよという人でも、「待ち時間がどれくらいか」がわかるなら、それに越したことはありませんよね。
そんな時に役立つかもしれないのが「リトルの法則」。
1961年、当時ケース・ウェスタン・リザーブ大学(アメリカ)に勤めていたジョン・リトル氏が発表した公式で、彼の名前から「リトルの法則」と呼ばれているものです。
数学や統計学の分野で「待ち時間」を予測する理論はそれ以前から考えられてきましたが、リトルの法則はこれをシンプルな公式で表したという点で画期的なものでした。
その公式とは次のように表されます。
W=L/λ
・W:待ち時間(分)
・L:列に並んだ時、自分の前にいる人数
・λ(ラムダ):並び始めて1分後、自分の後ろに並んだ人数
つまり、すでに前に並んでいる人数を、1分間に後ろに並んだ人数で割ることで、自分の待ち時間を予測できるというわけです。
より具体的に、例を挙げて計算してみましょう。
行列の待ち時間の求め方
たとえば、人気のラーメン店にできた行列での待ち時間を試算してみます。
自分が並び始めた時点で、20人の順番待ちの列ができていたとします。
それから1分の間に、自分の後ろには2人が並びました。
この場合の待ち時間をリトルの法則に当てはめて計算すると、20を2で割った「10」が、入店までにかかる分数と推定されることになります。
とても簡単ですよね。
ただしリトルの法則の精度は、行列の長さが一定に保たれずに伸びたり縮んだりする状況では下がってしまいます。
ラーメン店の例で言うなら、1分間に店を出る人数と1分間に列に並ぶ人数が常に同じでないと待ち時間を正確には当てられないということ。
人の行列は状況次第で伸びも縮みもするものですから、リトルの法則で求めた待ち時間はあくまでも推測値、目安と考えるくらいが良いかもしれません。
さまざまなシーンでの「リトルの法則」
ラーメン店に限らず、暮らしに身近なところでも気軽に試せそうなリトルの法則。
そもそもは経営上の諸問題を数学によって解決しようという研究分野「オペレーションズ・リサーチ」の理論であり、実は社会のいろいろな場面やビジネスの現場でさまざまに応用が試みられています。
以下にいくつか用例を挙げてみましょう。
店舗側が来店客の状況を分析
先ほどのラーメン店の例では客側の立場で待ち時間を計算しましたが、立場を変えてお店側が行列の状況把握に用いれば、新たに来店した人におおよその待ち時間を伝えたりすることもできます。
また、Lを店内にいる客数、λを一定の時間内に入店した人数にそれぞれ置き換えると、同じW=L/λという公式で来店客の平均滞在時間を求めることも可能です。
有料道路の料金所にできる車列を調整
ETCの普及によって緩和されてはきたものの、かつては有料道路の料金所といえば渋滞がつきものでした。
アメリカの一部の料金所では、リトルの法則の考え方を活かして1ゲートあたりの車列の台数の上限を設定、この台数を超えそうになったら閉じていた別のゲートを開け、ドライバーの待ち時間が一定の長さ以上にならないよう調整を図っていた例があるようです。
工場の作業効率アップを促す指標に
リトルの法則は人の待ち時間以外にも応用されます。
工場における製品製造ラインを例にとりましょう。
製品がひとつできあがるまでにはたくさんの工程がありますが、どの工程の投入口にも、材料やパーツ、途中まで組み上がったユニットなどが常に待機しています。
この状態を行列になぞらえて考えるわけです。
Lが待機中のパーツ数、λが1分間で待機列に追加されたパーツ数とすれば、W=投入されるまでの待ち時間が推定できます。
作業効率から見れば待ち時間は短いほうが良いですから、現場によっては、改善策の検討など、リトルの法則での現状分析をきっかけに時間短縮が図られていくケースもあるでしょう。
物流現場での「行列」と「待ち時間」
さて、ここからはいよいよ物流現場でのリトルの法則の話に入っていきます。
まず、物流倉庫内で「行列」「待ち時間」に相当するものといったら何でしょう。
「在庫日数」が、その一つに挙げられるのではないでしょうか。
Lを物品の在庫数、λを一日あたりの入庫数とすることで、W=「物品が倉庫内に置かれている日数」が算出できますよね。
当然ながら、この日数が長ければ長いほど在庫回転率は良くないということになります。
また、ピッキングされてきた物品が出荷のための検品を待つ間に滞ってしまう状態を思い浮かべる人もいるかもしれません。
理論上、ピッキング作業の速さと検品作業の速さが一定かつ等しければ貨物の滞留は起こらないはず。
しかし、熟達した各作業員がベストを尽くしたとしても、物品の滞留はほぼ確実に起こります。
ここでも、リトルの法則によって「1個の貨物が滞留する時間」を分析することが可能です。
この場合まず、ピッキング作業で1分間に処理できる貨物数を割り出し、λに入れます。
仮に60分で150個処理できるとしたら、150/60=2.5個がλになりますね。
L=滞留している貨物を仮に20個とすれば、20/2.5=8分が「貨物の滞留時間」です。
これもまた、長ければ長いほど作業効率の悪さが表れてしまっていることになります。
それでは、こうした分析を現場ではどう活かすべきなのでしょうか。
法則で求めた「待ち時間」の短縮を目指そう
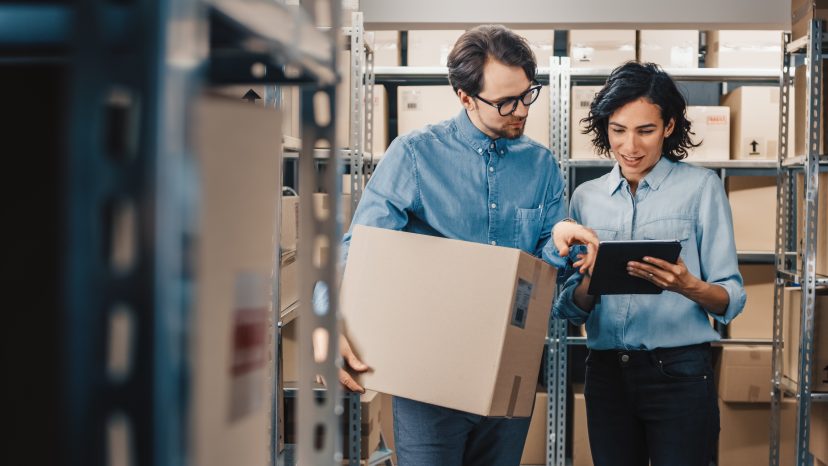
上に挙げたように、リトルの法則は物流倉庫作業における「待ち時間」の分析にも使えます。
それはある意味で、できるだけゼロに近づけたいムダな時間を可視化する数字です。
しかし数字が見えただけでは、そのムダを解消することはできません。
「問題を、問題として捉えるか否か」。
リトルの法則によって問われてくるのは、おそらく、工程を管理するにあたっての問題意識の有無なのです。
たとえば先ほど試算してみた「8分」という滞留時間。
これを「よし」としてしまえば、話はそこでおしまいです。
逆に「8分」をムダと捉え、時間短縮を図ろうとするなら、現状の工程間の改善すべきポイントがいろいろと気になってくることでしょう。
どこかに見直せる点はないか。処理速度を少しでも安定させられないか。
そうしたいくつもの取り組みにつながる契機として用いられるとき、物流現場におけるリトルの法則はその価値を発揮するということが言えそうです。
まとめ
今回は、「待ち時間理論」のひとつであるリトルの法則の基本を踏まえつつ、この数式を物流現場で活かす可能性について考えてきました。
数式というと、どうしてもとっつきにくかったり、普段の業務には縁遠いイメージがあるかもしれませんが、リトルの法則は発表から半世紀もの間、さまざまな場面で有用とされてきたものです。
自社の工程管理や作業のさらなる効率化を進めるうえで、課題や目標を見出すきっかけにしてみてはいかがでしょうか。