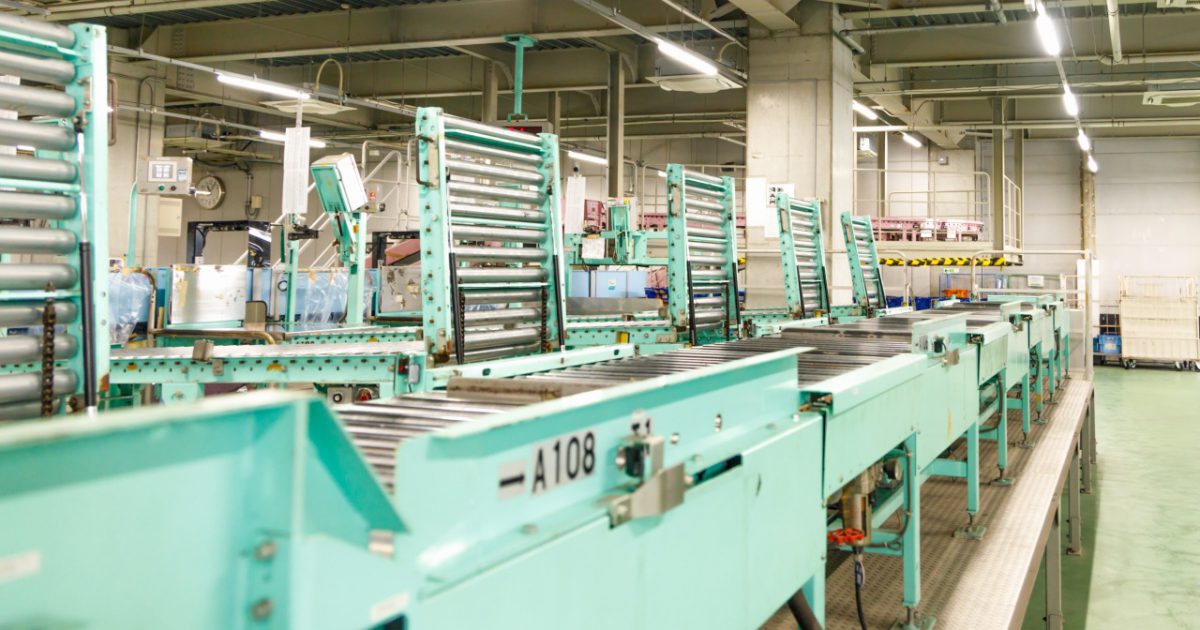
安全・品質
品質管理の基本!物流現場におけるQC7つ道具の考え方
物流現場でお勤めの皆さん、「QC7つ道具」というものをご存知でしょうか。QC7つ道具とは、品質管理における7つの分析手法を指します。もともと製造現場における品質管理から出てきたもので、「QCサークル」という職場内の小集団で品質向上・改善に取り組む活動と連動して確立、発展してきました。
この記事では製造現場から出てきたQC7つ道具をどのように物流倉庫内で転用・応用して使っていくかという視点から解説していきます。
安全・品質
2021.01.27
この記事では物流現場における特性要因図の使い方を解説いたします。
物流現場でなんらかの改善に取り組むとき、目の前の問題から着手していってしまいがちです。しかしその問題が本当に一番はじめに取り組むべき問題なのでしょうか。
見落としているもっと先に取り組むべき課題が他にもあるかもしれません。そのようなときに役に立つのが特性要因図です。
特性要因図はQC7つ道具の1つです。QC7つ道具とは品質管理における7つの分析手法のことを指します。特性要因図のほかにチェックシート、パレート図、グラフ、管理図、ヒストグラム、散布図、層別があります。
QC7つ道具については以下の記事で取り扱っておりますのであわせてご覧ください。
特性要因図とは以下のような図のことです。別名フィッシュボーンチャートとも呼ばれます。右側に改善したい課題(特性)を記入し、魚の骨のようにその原因となるもの(要因)を書き込んでいきます。魚の骨に見立てて、中央の線を背骨、背骨から伸びる線を大骨、次に中骨、次に小骨と呼びます。
大骨のより具体的な内容を中骨に、中骨のより具体的な内容を小骨に書き込んでいきます。
実はこの特性要因図の概念を提唱したのは日本人で、経営学者・工学者の石川馨教授です。
海外では石川ダイアグラム(Ishikawa diagram)と呼ばれていると自著で明かしています。(石川馨『TQCとは何か 日本的品質管理』,1981)
特性要因図は、品質における「特性」とその「要因」を整理する図という意味です。見た目が魚の骨に似ていることからフィッシュボーンチャート・フィッシュボーンダイアグラムなどと呼ばれることもあります。
もともとは製造現場における品質管理のために開発された道具ですが、さまざまな業界で汎用的に用いることが可能です。
特性要因図は問題の原因(要因)を探す道具です。品質における特性の要因はひとつではありません。探そうと思えば無限に要因を見つけることが可能です。
特性要因図は目についた問題から闇雲に手を付けるのではなく影響度が大きい問題から手を付けるための手法です。特性要因図を作成することで全体を俯瞰的に捉えることが可能になります。
特性要因図は完成したものをあとから第三者が見ても瞬時に読み解くのは難しいです。
MECE(もれなくダブりなく)な形の図を作ろうとすると制作の労力はグッと上がってしまいます。特性要因図は完成したものを誰かに見せるということは意識せず、「作る過程に意味がある」ということを参加者で共有してから制作しましょう。
その課題に関わるすべての関係者で議論するのが理想です。すべての関係者が課題の核となる問題点を共有することで、実際に手を動かして解決するフェーズがスムーズに進むようになります。
特性要因図は作る過程に意味があると述べましたが、最終的には完成した特性要因図を見ながら優先順位をつけるのがゴールです。ただし、特性要因図を作っただけでは定量的な評価を行うことはできないので、ディスカッションを行って直感的に優先順位をつけることになります。もしくは、影響が大きいのではないかという要因にいくつかのあたりをつけ、チェックシートなどを用いて定量的な評価ができるように調査を行います。とはいえ、そこから調査をはじめて集計・分析を行えるだけの時間的余裕があることはあまりないので、大抵の場合作業者が体感的に感じる重要度に従って優先順位をつけることになります。
特性要因図は完成した図から読み取れることはあまり多くはありません。関係者全員が議論をしながら特性要因図を作り上げていくことによって、関係者の中で「何が本当の問題か」ということのすり合わせができていきます。
さらに、現場でなんらかのトラブルが起きた際に、既に出来上がっている特性要因図を見ながら今回は何が原因だったのかを確認するツールとしても使うことができます。作業者がなんらかのミスを起こしたとき、管理者として原因を追求しようとしても「不注意で破損させてしまってすみません」など、謝罪に徹する作業者の方は非常に多いです。そういった場合にも一緒に図を見ながら、まず「作業者」の不注意が原因、ということを認めつつ、他の要素について、作業手順に問題はなかったか、現場環境にミスを誘発するような要因はなかったかということを探ることでミスを引き起こしている本当の要因を聞き出すことができるかもしれません。
特性要因図に見落としがあれば、随時書き足していきましょう。新しい要因を他の要因と比較・評価することで問題の重要度・優先順位をつけることができます。
特性とは、品質改善をしたいテーマのことです。ここでは特性要因図を作って改善したい特性であるため、課題になっていることと言い換えてもいいかもしれません。これを魚の頭に当たる部分に書き込み、何が課題なのかを明らかにします。
次に、特性の大骨を決めていきます。大骨は、要因の漏れがないように決める必要があります。
物流現場であれば作業者、現場環境、作業内容、商品特性の4つをベースとして考えてみるのがおすすめです。いったんこの4つでスタートして、足りなければ増やしてみるのがよいでしょう。
中骨・小骨はかぶりがあっても問題ありません。例えば「教えた人によって作業手順が違う」という小骨が「作業手順」の中骨の下にも、「マニュアル」の中骨の下にもついていて問題ありません。次々と出てくる意見を否定しないほうがはるかに重要です。
小骨で足りなければさらに骨をつけたしても大丈夫です。
パワーポイントで特性要因図を作ることができるテンプレートをご用意しました。
パソコン上で書き込んでいってもよいですが、A3サイズに空欄のままプリントアウトして手書きで書き足していくほうが手早く自由に書き込んでいくことができるのでおすすめです。
そこまで手のかかる作図でもないので最初からすべて手書きしたほうが自由度は高いのですが、この記事を読んでとりあえず一度手を動かして試してみよう、というときには役に立つはずです。
ぜひご活用ください。
安全・品質
物流現場でお勤めの皆さん、「QC7つ道具」というものをご存知でしょうか。QC7つ道具とは、品質管理における7つの分析手法を指します。もともと製造現場における品質管理から出てきたもので、「QCサークル」という職場内の小集団で品質向上・改善に取り組む活動と連動して確立、発展してきました。
この記事では製造現場から出てきたQC7つ道具をどのように物流倉庫内で転用・応用して使っていくかという視点から解説していきます。
パワーポイントで特性要因図を作ることができるテンプレートです。
無料でダウンロードできます。